Two Major Issues with Managing Safety Lifecycle Data
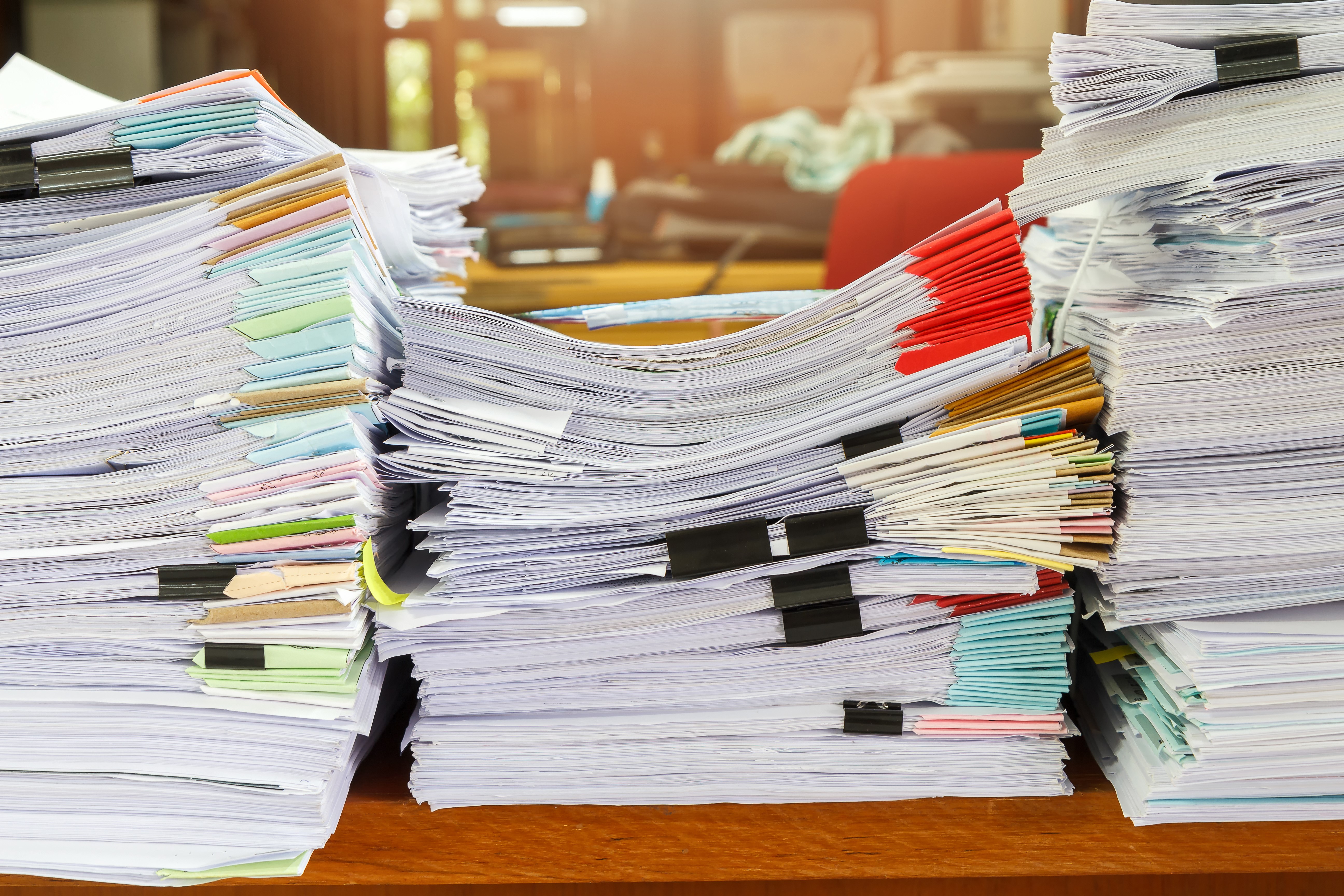
There are many issues with managing Safety Lifecycle data in a real plant environment. The fundamental problem is that the tools available in the plant are traditional and unsuitable for an effective Safety Lifecycle Management program. Especially for Instrumented Systems, much less other functions such as non-instrumented systems or relief systems.
Plants that manage the Safety Lifecycle generally have to resort to manual data gathering and retention procedures that are outside of what management perceives as their core tools. This results in systems that are very inefficient making it easy to develop gaps or become out of date. This is a very common issue in the process industry.
- Maintenance Management System (MMS)
There are very traditional Maintenance Management Systems that have been implemented by cost driven projects that are transitioning old home-grown systems to large commercially available systems. Implementation teams usually have directions– “If the old system didn’t do it, the new one shouldn’t either”. However, the old systems do not include instrumentation or new ideas such as Safety Systems that are needed.
The system is typically driven by Work Order Management, Warehouse stock management, and Maintenance Management of major equipment. Attempts to add Safety Instrumented Systems (SIS), Safety Instrumented Functions (SIF), field instruments and the like are exercises in futility. The system can’t handle the sheer volume and really can’t handle things that have a lot of inter-relationships. Furthermore, management typically does not support the effort required to input additional data into the MMS even if it is known the system can handle it.
- Instrument Database
Commonly used commercial Instrument Database applications define such things as instrument data sheets, loop diagrams, wiring, etc. They are typically used for large engineering projects, yet still have issues such as rudimentary maintenance functions and not able to support ongoing events. Attempts to force it to fit needs usually won’t work very well.
In effect, maintenance data for instrumentation is only as good as individual records. The MMS could be used for Work Orders and warehouse stock management, but not much else. All Work Order feedback, when existing, is usually manually entered text and seldom contains useful instrument work information.
- Process Hazard Analysis (PHA) Records
The Process Safety Group is usually responsible for facilitating PHA’s for the facility. This includes initial PHA/HAZOP, 5-year revalidations, projects, and in-house Management of Changes (MOC). They use a combination of commercial PHA/HAZOP applications, Excel spreadsheets, as well as both paper and electronic MOC check lists. All of this is typically kept in the group’s records, yet they are exceptionally hard to use for other purposes. The PHA/HAZOP applications also usually have draconian license restrictions which only allow the Process Safety Group to have access.
Every PHA/HAZOP and MOC checklist is usually kept in a separate file which causes major efforts to then find it. Requests for information can be met with a “Who wants to know?” response causing substantial delays in actually getting the information, if it is ever received.
Sometimes, master lists of Independent Protection Layers (IPL) that are identified in the LOPA’s do not correlated to actual plant assets, or even exist at all. The operations and maintenance personnel then have no real knowledge of what the IPL’s are. Also, they tend to lack knowledge of what hazards led to the requirements for the IPL’s to be there in the first place
- Document Management
Some facilities have a centralized document system that seems to work. Being able to access scanned or source files for just about any drawing or document in the facility can be useful. However, there is sometimes an unspoken rule that the document system would contain “engineering data only”. Documents are then to be stored only by Unit and document type. That would work if that’s all that is needed, but if not, don’t even think about asking for a list of documents associated with a piece of equipment, or a Safety Function.
- Independent Protection Layer (IPL), Safety Instrumented System (SIS) and Safety Instrumented Function (SIF) Management
It is becoming clearer that traditional plant management tools are not able to manage the Safety Lifecycle for Instrumented and non-Instrumented protective functions. Previously, there were no commercially available data management tools, so the effort got reduced to setting up a series of folders on a facility network drive. In attempt to capture a “dossier” of protective systems, scanned copies of widely dispersed data such as PHA/HAZOP/LOPA documents, SRS’s, test procedures, design documents, and data sheets were stored. Other folders are typically created to provide a place to store operationally related things like scanned copies of completed test procedures and Excel spreadsheets of various events.
This process was used parallel with existing documentation systems because it was the only way that all the relevant information could be collected and made accessible. In theory, these documents were available in other systems yet finding them would be a scavenger hunt if the documents weren’t collected separately. The system is very labor intensive as manual labor is required to collect all the relevant documents and then electronically file them. It was something of an underground effort, as site management didn’t really appreciate the value of the data. Furthermore, this systems longevity depended heavily upon not having a poor quarter of financial performance.
It can be very difficult to manage the Safety Lifecycle within a plant that only has the traditional commercial Process Safety, Maintenance Management, and Documentation applications that you typically find in any general operation. Some facilities have structured their own system by just filing the relevant documents in a parallel network drive folder, but that isn’t a permanent solution. Safety Lifecycle management requires a separate purpose –built application for proper Safety Lifecycle Management.
Read more about Justifying Investment in a Safety Lifecycle Management Platform
Rick has a BS in Chemical Engineering from the University of California, Santa Barbara and is a registered Professional Control Systems Engineer in California and Colorado. Rick has served as a member and chairman of both the API Subcommittee for Pressure Relieving Systems and the API Subcommittee on Instrumentation and Control Systems.