The Biggest Problem with Safety Lifecycle Management Roles and How You Can Fix It
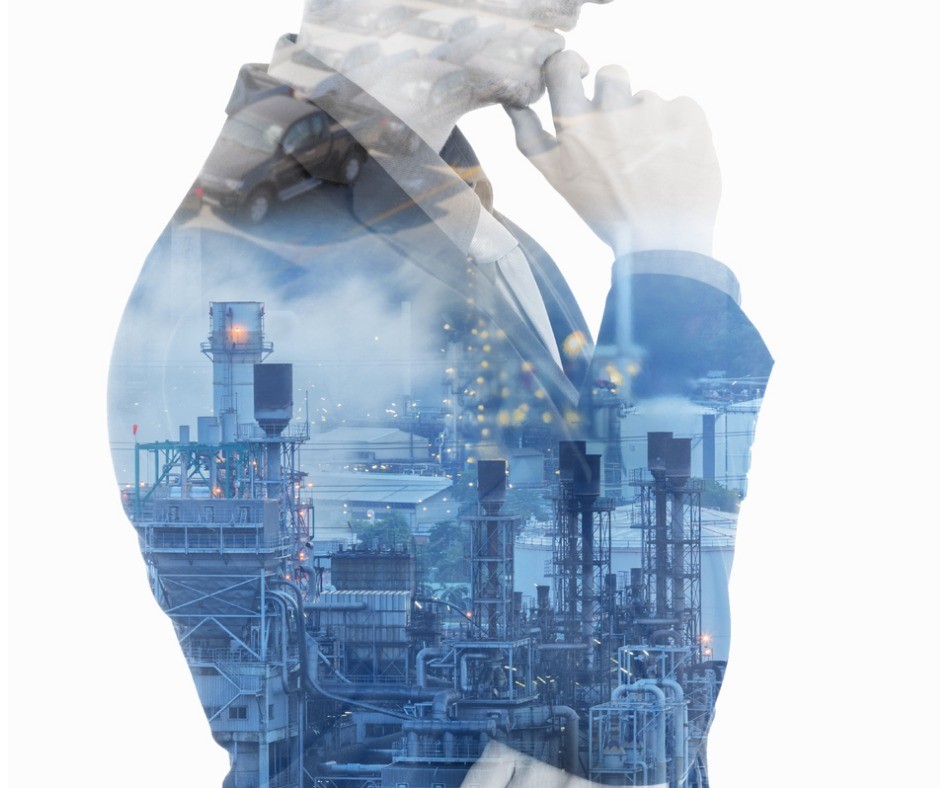
The problem:
Many organizations are trying to figure out how to manage the Safety Lifecycle. Leadership will often end up just appointing someone as “the SIS guy”. Sometimes the role is given a fancy title, but the intent is to assign the issue of the entire Safety Lifecycle to someone. That someone is usually in engineering, who may or may not actually have the skills to take on the task. Leadership then thinks they’ve done all that is necessary. The poor person who gets handed the responsibility usually doesn’t have any authority to go along with it, but they are somehow expected to “make it happen”. The organizations that try this approach typically fail.
There are enough responsibilities to go around. An effective Safety Lifecycle Management program recognizes this and clearly identifies who has what responsibility focusing on each area of the Safety Lifecycle. If there is a central authority, they are given a very big management stick to hold every department fully accountable.
Three main phases to consider:
1.) Requirements Identification
This is where the Process Safety function in an organization has responsibilities that include:
- Define Risk Management Standards
- Facilitate HAZOP and LOPA Studies
- Clearly communicate results to the Engineering, Operations and Maintenance personnel
The Requirements Identification process continues as modifications are made, new processes are added, and periodic re-validations are needed. Other groups with Safety Lifecycle responsibilities also fully participate in the identification of protective system requirements but the Process Safety function is in charge of it.
2.) Specification, Design, Installation
This is typically an Engineering Group that translate the basic requirements from the Process Safety function into real designs, as well as implement them. The responsibilities include:
- Prepare the Safety Requirements Specification (SRS)
- Assure that the design meets the SRS
- Follow the detailed design
- Inspect and validate testing
Along the way they are also responsible for assuring that all testing and maintenance procedures are prepared and approved. Also, engineering personnel will often be responsible for monitoring the performance to identify any changes that are needed to continue to meet the requirements of the design.
This requires that events such as faults, failures, bypasses, demands, and testing, etc. be reported to the personnel responsible for evaluating performance. The personnel that assess protective system performance are also responsible for reporting the results to all groups that have related responsibilities, including Site Management.
3.) Ownership
This starts during design while Operations and Maintenance procedures are being prepared. Operations and Maintenance are trained and qualified personnel.
The Operations responsibilities include:
- Ensure that protective systems are operated in accordance with SRS requirements and operating procedures
- Record all operational related events
- Report all events to the personnel responsible for assessing the protective systems performance
- Monitor testing requirements to make sure that all required testing is performed on schedule and according to testing procedures
The Maintenance responsibilities include:
- Perform testing and repairs as required by the schedule and procedures
- Any repairs needed between testing intervals
- Maintain all testing and repair records and report them to the personnel responsible for assessing protective systems performance
- Schedule and plan period testing
The Fix
Because the Safety Lifecycle is a multi-organization endeavor, a collaborative approach is ideal. The need for communication among various responsible groups requires clearly identified roles of responsibility for each area of the Safety Lifecycle. The Safety Lifecycle is not something that can just be handed off to anyone. It’s a deep organizational commitment that involves qualified personnel doing specific parts of the job. Management also needs to provide proper oversight to assure that the process is followed as required.
Rick Stanley has over 40 years’ experience in Process Control Systems and Process Safety Systems with 32 years spent at ARCO and BP in execution of major projects, corporate standards and plant operation and maintenance. Since retiring from BP in 2011, Rick formed his company, Tehama Control Systems Consulting Services, and has consulted with Mangan Software Solutions (MSS) on the development and use of MSS’s SLM Safety Lifecycle Management software.
Rick has a BS in Chemical Engineering from the University of California, Santa Barbara and is a registered Professional Control Systems Engineer in California and Colorado. Rick has served as a member and chairman of both the API Subcommittee for Pressure Relieving Systems and the API Subcommittee on Instrumentation and Control Systems.